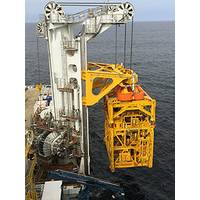
First Subsea Gas Compression Plant On Line
. “High-quality, regular maintenance of the subsea modules will also be performed here, helping ensure operational excellence for Åsgard,” Espedal Kindem said. The Midgard and Mikkel gas reservoirs have been developed using subsea installations. The two gas compressors now installed on the seabed are located close to the wellheads. Moving the gas compression from the platform to the wellhead substantially increases the recovery rate and life of the fields. Prior to gas compression, gas and liquids are separated out, and after pressure boosting recombined
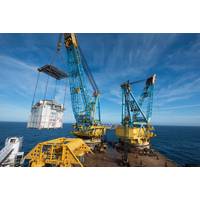
MTR100: Venture into the Norwegian Subsea Valley
, “the next big thing.” Company R&D worldwide now includes 8,500 staff and a $1.5 billion budget. A subsea electrical power JIP with Statoil (akin to GE Oil & Gas’s and Nexans’s) is understood to be costing $100 million. A 100 MW seabed power supply for large pumps and gas compressors is the goal. Prototype production is underway of a 100 MW transformer and variable speed drive capable of changing loads and able to power a seabed compressor from 100 km. Deliveries are seen by 2019. Operators see $500 million in OPEX savings for the CAPEX, plus greater recovery rates.  
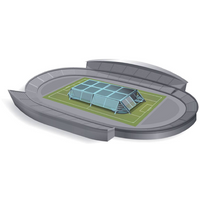
Subsea Energy Production Beats Topside Method Says ABB
subsea vision However, transferring energy over such distances with acceptable losses is in itself a challenge. To solve some of the challenges ABB and Statoil recently entered a joint industrial program (JIP), that entails development of technologies to supply electrical power for subsea pumps and gas compressors, as well as providing power conversion systems. The JIP will provide solutions for transmission of electrical power up to 100 megawatts (MW) over a distance of 600 km and to depths of up to 3,000 m. The JIP is the outcome of an extensive subsea electrification study performed by Statoil and
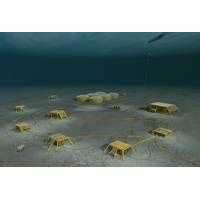
Ultra-Deepwater & Remote Subsea Factories R&D
ABB has entered a US$100-million research and development joint industry program (JIP) with Statoil to develop solutions for transmission, distribution and power conversion systems designed to power and control subsea pumps and gas compressors at depths of 3,000 meters, and over vast distances. The agreement is seen as an important step on the path to develop complete subsea oil and gas producing facilities. Statoil is leading the JIP on behalf of other participating oil companies, while ABB is responsible for developing the new technology. It follows an extensive subsea power study executed by
Statoil, ABB Enter Subsea Technology Agreement
oil companies, with ABB as the technology developer. The agreement follows a large subsea electrification study executed jointly by Statoil and ABB during 2012. “The JIP will develop technologies needed to provide electrical power to subsea pumps, electrical submersible pumps and subsea gas compressors for projects on the Norwegian continental shelf, in the Gulf of Mexico and other places around the world,” said Statoil senior vice president for research, development and innovation Karl Johnny Hersvik. Subsea pumping and gas compression contribute to improved utilization of the oil
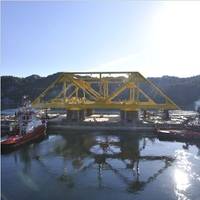
Aker Delivers Åsgard Template to Statoil
field seabed to form the base of the world's first subsea gas compression facility. It is the largest template manufactured by Aker Solutions, measuring 74 meters in length, 45 meters in width and 26 meters in height. Reservoir pressure at gas-producing fields drops over time, reducing output. Gas compressors are used to raise the pressure and extend the life of a field. Such compressors have typically been installed on platforms over sea level. Placing the compressors on the seabed and near the wellheads improves recovery rates while reducing overall capital and operating costs. Subsea gas compression