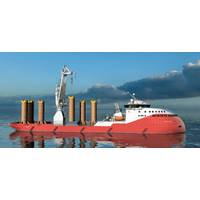
Ulstein Introduces New Subsea Vessel for Offshore Energy Market
market, the ULSTEIN SX232 features an optimizes hull based on the ULSTEIN TWIN X-STERN design.The vessel is equipped with smart power and propulsion system developed to minimize energy consumption during DP operations and an integrated energy recovery system utilizing all the waste heat in the machinery systems, including cooling water and exhaust.According to Ulstein, this will enable the ULSTEIN SX232 to reduce emissions and operational costs while enhancing performance, safety, and comfort.The design of the vessel has been developed to include versatile fuel options and a battery energy storage
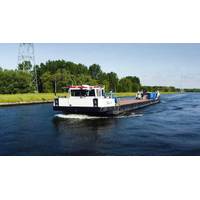
Barge Completes Autonomous Navigation Test in Busy Belgian Waterways
project, part of the EU research program Horizon 2020. AUTOSHIP is a collaboration between KONGSBERG and Norway’s leading research organisation, SINTEF, as well as several European partners.The aim of the AUTOSHIP project is to test and develop fully autonomous navigation systems, intelligent machinery systems, self-diagnostics, prognostics and operation scheduling, as well as communication technology enabling a prominent level of cyber security and integrating the vessels into upgraded e-infrastructure.The successful test of the Zulu 4 barge verifies the maturity of key enabling technologies
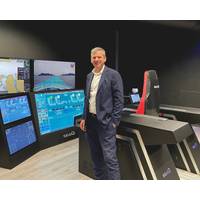
New Product: SeaQ Remote for Autonomous Ship Ops
on our long and proven experience in the shipbuilding industry,” said Vard Electro’s CEO Andrea Qualizza.Accoding to the developers, SeaQ Remote extends smart data-driven functionality to operational technology (OT) in the vessel hull as it enables remote operation of existing machinery systems such as engines, propellers and thrusters. Machinery is connected by sensors that can stream real-time data via the cloud to an onshore control center. Merged data from these sensors on a unified user interface provides a smarter way to gain an enhanced awareness of the status of onboard systems
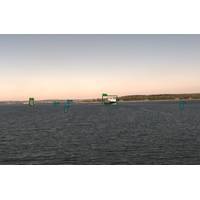
Partnering on the Digital Ship: Inside Denmark’s ShippingLab
offshore operations, and boats for firefighting:“Autonomy in these cases will once again increase safety by removing humans from dangerous environments, diminish energy consumption, and standardize operations. Digitalization in the form of, for example, advanced condition monitoring of vessel machinery systems can provide vessel owners with a large amount of information and give operation and maintenance companies information about how the vessel is operated, enabling more efficient and possibly cheaper maintenance,” said Galeazzi.“A more digitalized ship is potentially a more transparent
ABS Makes it Safer to ‘Walk to Work’
sensing devices that compensate for heave, pitch and roll motions enabling the end of the gangway to remain geostationary relative to the platform, creating a safe and stable walkway. The Guide provides requirements for offshore access gangway system certification, including structural strength, machinery systems, contingency management, system recovery and redundancy, safety and communications, and regulatory requirements. These requirements apply to both active and passive motion compensated systems. In addition to the Guide, ABS offers a provision for offshore access gangway systems to be qualified
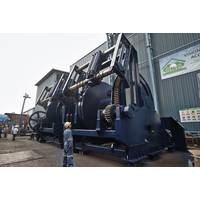
MTR 100: Jebsen & Jessen Offshore Pte Ltd.
of solutions to support customer’s marine and offshore needs. Its 400 strong workforce includes in-house engineering, project management teams and a dedicated service and response unit. The company is one of the largest manufacturers of offshore winches, cranes, A-frames, and complex deck machinery systems in Asia. In Singapore, the company has three facilities situated by 11 Tuas Crescent. This Tuas facility carries out the final assembly and FAT of AHC Cranes/Winches; Offshore Cranes; LARS and other offshore equipment that has testing for crane of up to 6,000MT and winches to 600 Ton SWL respective
Rolls-Royce Delivers Far Sleipner
and propulsion. Børge Nakken, Farstad Shipping, Vice President Technology & Development, said: “The DP3 positioning system onboard Far Sleipner ensures that the vessel stays in position, even in the event of an unforeseen situation, for instance if one out of two separate machinery systems fails. This enables the vessel to complete its task in a safe and efficient manner.” The main difference between a DP2 and DP3 dynamic positioning system is related to redundancy and tolerance for system failure. All key components of the systems are doubled up in a DP3 system. This
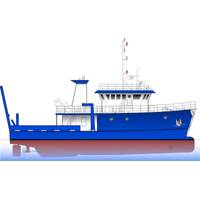
JMS to Design Research Vessel for Virginia Institute of Marine Science
coastal-science studies including fish and invertebrate sampling; bottom geological and benthic coring; deployment and retrieval of data buoys; heavy mooring, seismic and bathymetry surveys; mid-water and trawls; CTD and other vertical water-sampling deployments. The hull, propulsion and machinery systems will be designed for quiet operation for acoustic survey work and be equipped with state of-the-art technology with an emphasis on energy efficiency. jmsnet.com vims.ed