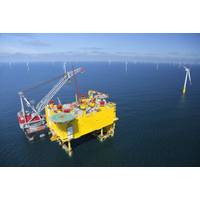
OEG’s Bluestream to Service TenneT’s Offshore Grid Connection Unit
Bestream Offshore, one of the companies in OEG Energy Group’s subsea division, has secured a contract by TenneT for the retrofit installation of a corrosion protection system for the SylWin alpha offshore converter station for the offshore grid connection SylWin1 in Germany.The award is for the subsea installation of an Impressed Current Cathodic Protection (ICCP) system to replace the existing faulty ICCP system.The replacement of the existing system includes the decommissioning of outdated cables and debris which cause system interference, alongside a pre-survey which will be conducted using a
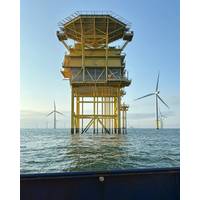
Acteon Marks First-Year Milestone at German Offshore Wind Farm O&M Job
inspection contract with Siemens Gamesa Renewable Energy (SGRE) for the 228 MW Butendiek offshore wind farm in Germany.During the first year, Acteon conducted annual subsea foundation inspections using remotely operated underwater vehicles (ROV), array cable and foundation seabed surveys, and corrosion protection surveys for the wind farm, located approximately 32 km west of the island of Sylt in the German sector of the North Sea.The work was performed by UTEC, a brand within Acteon’s geo-services business line, and included a multibeam echosounder seabed survey of the array cables and foundation
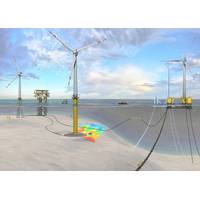
Acteon Bags O&M Contract for 228MW German Offshore Wind Farm
Island of Sylt in Germany.Led by UTEC, the work will be supported with services from Acteon brands Clarus, Deepwater and Seatronics.Under the contract, Acteon will perform annual subsea foundation remotely operated underwater vehicle (ROV) inspections, array cable and foundation seabed survey, and corrosion protection survey covering the wind turbine generators and the offshore substation (OSS).UTEC will perform a multibeam echosounder (MBES) seabed survey of the array cables and OSS/WTG scour protection while Deepwater's POLATRAK Drop Cell - DC II equipment will be used for the corrosion protection
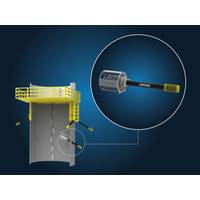
Subsea Monopile Corrosion Protection
Corrosion and BlueStream launched ICCP-SAM, touted as sustainable corrosion protection of XX(X)L monopile foundations. ICCP-SAM is designed to remotely install ICCP anodes on monopile foundations of all sizes, anywhere on the foundation and even in the roughest ocean conditions.The ICCP-SAM (Subsea Assembly Method) is compact and can be transported and deployed with minimal resources from the topside of the offshore foundation. It is operated remotely and maneuvers the anode underwater into the designated foundation entry hole. The anode is then secured to the foundation using the same tool.
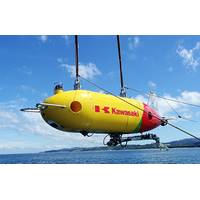
Kawasaki's AUV Used to Inspect Coating Defects on Subsea Pipeline
Awaji Island from August 30 through September 2, resulting in the successful measurement by LTCP integrated with SPICE of the electrical potential of subsea pipelines, Kawasaki said.Trial Participants(TotalEnergies,Kawasaki and Support Company)First, for this offshore test, simulated pipes and a corrosion protection system were placed on the seabed under the supervision of TotalEnergies."In the test, SPICE – utilizing its time-tested, excellent pipe-tracking capability and highly precise autonomous control of the robot arm – successfully performed measurements of electrical potential
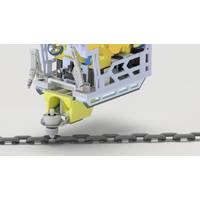
Imenco Launches Offshore Mooring Chain Corrosion Protection Tech
Imenco Corrosion Technology (ICT), a division of Imenco, has launched what it says is a transformational mooring chain cathodic protection technology, named Pacu.Initially designed for deployment on FPSO mooring chains, the system, Imenco says, is equally applicable to any mooring system such as those on floating wind platforms or offshore aquaculture installationsImenco says that the solution, made up of its Piranha clamp and an integrated bracket-mounted sacrificial anode, slows the rate of corrosion significantly and prolongs the life of mooring systems."Currently, the unpredictable rate of
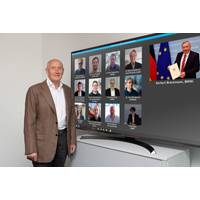
German Government Funds Autonomous Subsea Robotics System Development Project
contribute the development of inertial navigation systems and the method for autonomous docking of the system underwater.The University Medical Center Freiburg will focus on the development of electric field sensors that can cope with the harsh underwater environment and measure highly sensitive corrosion protection.GEOMAR Helmholtz Centre for Ocean Research Kiel specializes in all relevant aspects of modern marine science. The institute will develop the AUV’s camera system and provide test platforms for the systems
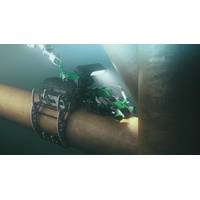
Subsea Robots in the Splash Zone
the North Sea, it is common to assume that structural details located below or in the splash zone are not accessible for inspection and repair.” The splash zone is defined in DNVGL standard, ST-0126.“Inspection of structures in the splash zone and below water focuses in addition on the corrosion protection systems (steel wall thickness, anodes, coating, etc.), marine growth and scour protection.” Yet, OceanTech’s tools do that hazardous work. The iCon robot addresses these and subsea structures as well, starting with risers that could lose buoyancy if fouled by marine life: they
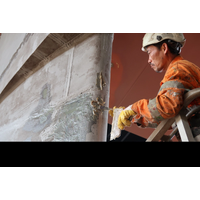
Performing Coating Systems for Different Applications
extraordinary. This is the effective alternative to metal facing or very expensive alternative fillers. And because it is part of the Subsea Industries family, it is fully compatible with our coatings.EcolockEcolock is used on stationary offshore units. The main benefit of the coating system is corrosion protection and the possibility to clean it. These units are designed to stay on location for 15, 20 and even up to 30 years. Hull integrity and corrosion protection is a major thing. Class demands an underwater inspection twice every five years to see if the hull is in good shape. So the hull must be