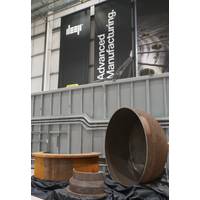
AiP Granted for Additive Manufacturing of Pressure Vessels for Human Occupancy
for pressure vessels for human occupancy.With 20 Wire Arc systems at its Advanced Manufacturing Centre of Excellence in Avonmouth, UK, DEEP Manufacturing operates one of the largest concentrations of Wire Arc Additive Manufacturing (WAAM) systems globally.WAAM enables the manufacture of large-scale metal components with complex geometries. Unlike powder based additive manufacturing, WAAM uses an electric arc to melt wire feedstock, which gives the end product a higher level of material quality.Compared to traditional manufacturing techniques, such as forging, WAAM offers greater speed of production, along
World First: Patrol Vessels Deploy 3D Printers
can provide.Minister for Defense Industry, the Hon Melissa Price MP, congratulated the Charles Darwin University’s Advanced Manufacturing Alliance, along with industry partner SPEE3D, for producing the cutting edge and uniquely Australian capability.“This high-tech machinery enables metal components to be produced quickly and efficiently, meaning our ships can get back on the water without delay,” Minister Price said.“Benefiting both the Navy and industry, the knowledge transfer gained using this capability also positions the Advanced Manufacturing Alliance to pursue further
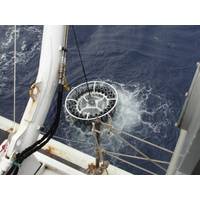
Case Study: Cables in Underwater Missions
at much lighter weight, while also eliminating metal contamination.Future useUS GEOTRACES has achieved the capability to lower the carousel deeper than ever before without weight concerns. The researchers can collect more samples faster and there is virtually no risk of contamination from exposed metal components.The organization has now used the custom cable for dozens of missions, in regions as diverse as the Arctic to the tropical waters of Polynesia. It has proven ideal for the expeditions, carried out every two years since 2008. It is set to be deployed again in 2021. Near identical cables are now
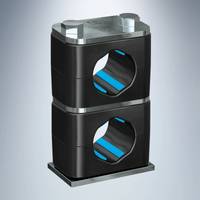
Stauff Clamps Allow Multilevel Installation
to multiple customer requests to complete the product line in this way. Installers and users benefit from the increased flexibility in the design and layout of pipework systems, because several lines running close together no longer have to be positioned side by side. As with all recommended metal components in connection with ACT clamps, the safety locking plates as well as the stacking bolts are also of 1.4401 or 1.4571 materials. At Stauff, in contrast to regular stainless steel components, contamination through metallic and non-metallic particles during production, processing and storage is