Lander Lab 8: Titanium and Ocean Landers
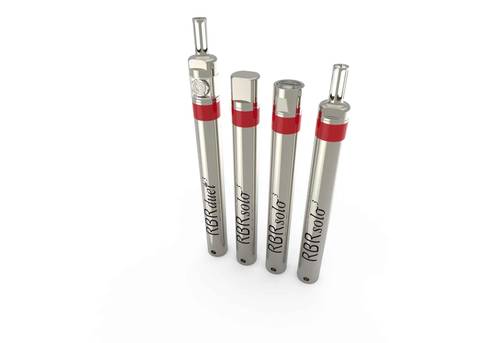
Figure 1: RBR compact, lightweight titanium housings for deepwater temperature and pressure loggers. (Photo courtesy of Keith Johnstone, RBR Ltd, Ottawa, ON, Canada).
Titanium and Ocean Landers
Titanium is an ideal oceanographic material with high strength, low density, and excellent corrosion resistance. It is the fifth most abundant material in the Earth’s crust, with properties between aluminum and steel. The production of titanium was initially developed to meet the needs of the aerospace industry, while the ocean industry benefitted from cross-over adaptation.
The principal alloys used in unmanned undersea systems are 1) Grade 5, Ti-6Al-4V (6% Aluminum, 4% Vanadium) and 2) Grade 2, commercially pure titanium (99% pure). Many machinists prefer the higher strength Ti 6-4 alloy (Grade 5) as it provides better finishes compared to the softer commercially pure Grade 2 unalloyed material. Titanium has a machinability index similar to that of stainless steels.
Cost and availability of the material has limited the wider use of titanium. Still, titanium has important application in Ocean Landers. Long duration landers may use titanium fasteners for assembly, the threads lubricated with zinc oxide paste to prevent galling. Other precision elements, such as sensor heads and instrument housings require no ongoing maintenance (see Figure 1).
Titanium’s corrosion resistance comes from a dense and tightly bound oxide layer that forms in a matter of a few minutes in air. The titanium oxide film resists attack by chloride ions in seawater, making the metal highly resistant to corrosion fatigue and corrosion cracking. This allows the material to be deployed for long periods of constant immersion without fear of degradation.
Titanium is non-magnetic, providing opportunity for through-hull magnetic coupling to sensors or Hall-effect switches for control.
Sourcing (DFARS) and Material Assay Certifications
Right up front: Buyer beware of where your titanium comes from. The high temperature (1620°F/880°C) metallurgical process requires time and an inert environment to develop the proper body-centered cubic crystalline structure. Improper billet manufacturing can result in parts that will fail prematurely.
Importantly, an assay based on XRF (X-ray fluorescence) can show a sample has the proper alloy elements in the correct proportions, but cannot confirm the proper crystalline structure.
I have personally experienced Grade 5 Titanium 6-4 material, improperly created at a foreign mill and inadvertently inserted into my production run. The material had the aluminum on one side of the bar, and the titanium on the other. This created a Ti-Al battery driven by galvanic potential. It was the first time I saw titanium corrode badly. The sensor body later passed the XRF (X-ray fluorescence) test, confirming it was Grade 5. It’s level of corrosion suggested something else.Figure 2: Corrosion of non-DFARS Titanium 6-4. The aluminum rich side corroded due to galvanic action. (Photo by Kevin Hardy, Global Ocean Design).
To help avoid poor Ti 6-4 material, end users must specify material sourced from “U.S. Mill or DFARS Only” in addition to material assay certification “Material Certs Required”. “DFARS” is the “Defense Federal Acquisition Regulation Supplement”. The list of DFARS nations is rather lengthy. As a first-order check, if the material assay certification is in any language other than English, you may have a serious problem and need to double check.
Specifying Grade 2 unalloyed titanium provides a better shot at getting excellent corrosion resistance at the cost of strength. I still call out “DFARS Only” in addition to requiring material assay certifications. There’s always the possibility that the wrong material is delivered with the certs from another run, but that requires diligence by and trust in your vendor. It helps if your vendor is ISO 9001 certified.
The reader is referred to the SME text “Tool and Manufacturing Engineering Handbook, Volume III, Materials, Finishing and Coating” for further discussion of Titanium metallurgy and fabrication.
Galvanic Series and Isolation
While it is good practice to avoid joining dissimilar materials, occasionally designers are faced with that challenge. It is important to recall that corrosion requires both an electron path and an ion path. Seawater is assigned the role of ion path. Isolating dissimilar materials with a non-conductive material breaks the electrical path, and thereby the galvanic cell. I have used flanged Delrin washers to isolate titanium fasteners from an aluminum frame. The frame has survived multiple year-long deployments without harm. I tried a similar approach with connectors of one material into a housing of another material using Delrin or Peek insulators (Figure 3).Figure 3. A brass MCBH bulkhead connector is isolated from an aluminum housing using a two-part Delrin insulator. The adapter assembly is (left-to-right) Delrin internal/external threaded insulator, Delrin adapter plate, and brass adapter plate. The combination has been tested to 10,000psi. (Photo by Kevin Hardy, Global Ocean Design).
Tests in early 1965 of Titanium 721 at the Naval Applied Science Laboratory showed signs of stress corrosion cracking. Ti-6AL-4V ELI grade (Extra Low Interstitials) was developed to have more resistance to this failure mode.
To manage costs, lander frames can be made from FRP structural elements, with side panels from HDPE, reducing cost and weight. Lifting bales are preferentially made of aramid fibers such as Kevlar, as they are lighter, stronger and can tolerate flex cycles normally experienced on recovery better than materials that are prone to work hardening.
Machining and Fabrication
Titanium fabrication requires an appreciation for the unique characteristics of the metal including: lower modulus of elasticity, lower ductility, low thermal conductivity, a tendency to gall, and a higher melting temperature coupled with a sensitivity to welding contamination. Welding requires shielding from air using Argon or Helium gas shielding techniques to avoid brittle welds. Galling can make tapping difficult.Figure 4. PREVCO Subsea 6000m depth rated titanium subsea Enclosures (Photo Courtesy of John Head, Prevco).
Anodizing Titanium
Titanium can be anodized. One patented process is called “Tiodize”. The surface growth is ranges from 20-200nm, little enough that no machining tolerance is required. Titanium anodize is suggested for threads that would otherwise gall. The use of zinc oxide lubricant is still recommended. While the anodize oxide is transparent, the parts can appear to have vivid rainbow-like colors due to interference coloring.
Bonding
Titanium’s dense oxide layer creates a low surface energy substrate that is difficult to bond to. The oxide layer can be abrasively blasted then primed within 2-3 minutes to create a satisfactory bonding surface.
Casting and 3D Printing
Casting of titanium parts is done in an inert atmosphere for reasons noted above. Laser sintering of titanium has been shown as a practical 3D print process, but also requires an inert atmosphere. Both have less strength due to porosity and lack of grain structure found in wrought material.
Acknowledgements: The author gratefully acknowledges the contributions of Michael May, Decisive Testing; Mike Gomper (Clint Precision Manufacturing); Reed Jackson (RJ Machine); Rob Klidy, Manager, Scripps Institution of Oceanography/UCSD Machine Shop, Stephen Dexter “Handbook of Oceanographic Engineering Materials”; R. Frank Busby “Manned Submersibles”.